Don’t let a slab leak get the best of you! Early detection is essential to preventing very bad damage.
A slab leak, also known as a foundation leak or concrete slab leak, is a plumbing industry term for a leak within piping below the concrete floor of older homes or businesses. Slab leaks are an issue in areas with a lot of ground shifting and can quickly become a very costly problem. Not only does a slab leak waste an excessive amount of water, but a leaking pipeline system can quickly cause significant damage to the foundation of your building, not to mention compromise the safety of your entire structure.
When your restaurant or business isn’t getting enough hot water, it might not be a problem with your water heater – it could be a slab leak on the hot water piping! Since slab leaks happen below a building’s thick concrete foundation, they are challenging to detect and fix. Nevertheless, they are very common, especially in areas where the ground soil is subject to shifting, settling, or earthquakes. Slab leaks should be addressed immediately so they don’t cause water damage or issues with a building or home’s concrete slab foundation. Remember: the longer you wait to fix a slab leak, the more money you may spend!
Additionally, slab leaks can be like snowballs that turn into avalanches: where there’s one crack or leak, more will usually follow. Repairing one slab leak can increase pressure on the pipes down the line (especially weak points like elbows), causing more leaky pipes immediately and over time. When found in hot water lines, slab leaks can also damage your water heater and prevent hot water from getting to your faucets. While slab leaks can happen on any underground piping in a building, they’re a particular nuisance on hot water lines (often misdiagnosed as a water heater issue when, in fact, that is not the case).
Reliable Water Services’ Sales Manager in Indiana, Chad Spurrier explains, “When water escapes in a slab leak situation, your hot water is constantly flowing and causing your water heater to fire. That constant firing reduces the life of your water heater. If the hole in your piping is large enough, your water heater can’t keep up. The water heater will stay fired and never shut off, but you still won’t get enough hot water flowing through your faucets.”
What Causes Slab Leaks?
Like all plumbing and building infrastructure, water lines and piping systems will break down over time. Still, several additional factors can cause damage to the pipes beneath your concrete foundation. The cost of your concrete slab leak repair will depend on the type of fix it needs.
Here are a few of the most common causes of slab leaks:
- Electrolysis: Electrolysis is a chemical reaction between copper piping, soil composition, and electrical current that can cause pipe corrosion and leaking.
- Improper Wrapping: Sometimes, exposed piping isn’t wrapped correctly when installed. Water running through the system can cause the pipes to move slightly. This is especially true in exposed hot water lines where the expansion and contraction from temperature changes can damage the pipe and cause a leak.
- Kinked or Nicked Line: When a water pipe is damaged, either during the original faulty installation or by someone doing work on the pipes or concrete after the fact, a weak spot can be created in the line. When combined with temperature changes, time, corrosion, and other factors, this weak spot can wear through and cause the pipe to fail, resulting in a leak.
- Ground Shifting: Concrete building foundations are susceptible to cracking and bowing over time as the surrounding ground shifts due to natural soil erosion and settling, seasonal temperature fluctuations, flooding, or earthquakes. The weight of the building on top of the foundation can also cause additional strain. Over time, all that shifting will eventually break water lines.
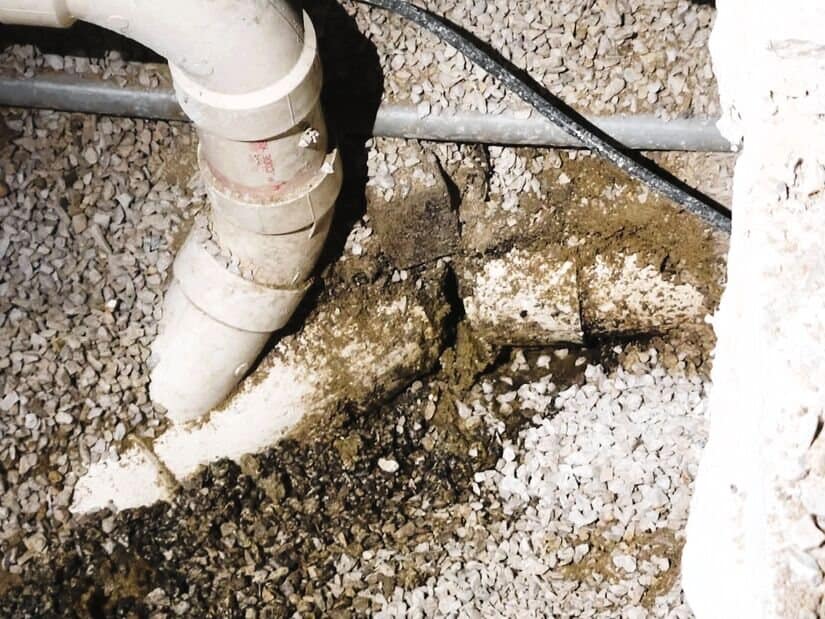
Signs of a Slab Leak
When water lines begin to leak, there can be some warning signs that you may notice, like:
- Loss of high water pressure/sudden low water pressure
- The sound of running water, even though all water is turned off
- Toilets flushing slowly or getting “clogged” frequently
- Hot spots or warm spots on the floor
- Cracks in walls or floors
- Mold and mildew or excessive moisture underneath carpets
- Water on the floor
- Wet baseboards
- Wet planters near the building
- Water coming out below the water heater, but the platform is dry
- Sudden, unusually high water bills
Slab Leak Detection
If you suspect a slab leak, you should hire professional help immediately. A skilled technician can find and diagnose your problem using proper modern detection and identification tools. If they’re doing things right, they’ll save time and money while minimizing property damage. Sometimes, slab leak repairs can be done with only a single tile needing to be moved and replaced.
A company specializing in slab leak detection will use one of several non-destructive detection techniques, such as:
- Acoustic Survey: Electronic amplification equipment with a microphone designed to “hear” leaking sounds, even through thick concrete flooring, is used to pinpoint the exact source of the leak.
- Line Tracing Equipment: Electromagnetic pipeline locators enable technicians to visualize the layout of the copper water lines and determine the location of the leak within the piping system.
- Isolation: Both ends of the leaking plumbing pipes are exposed, and the technician stops the leak. The pipe is then replaced after the leak has been appropriately identified and capped and is no longer leaking.
- Hydrostatic Pressure Testing: When pressure is added to the system, leaks are exposed by filling the underground pipes with dyed water. If there is a pressure loss, then there’s definitely a leaking pipe in the system, and the colored water will help to determine precisely where the leak is located.
- Thermal Imaging: Using heat-detecting thermal imaging technology, a professional plumber can visualize where the hot water pipes are leaking and determine the location of the plumbing leak.
Slab Leak Solutions
Unfortunately, slab leak detection, repair, and subsequent foundation repair can be costly. However, the safety and functionality of your structure depend on accurate detection and efficient corrections. There are several different repair options that your licensed plumber may suggest. These include:
- Spot Repair: The pipe is repaired by opening the slab only in the area around the leak.
- Re-Pipe or Reroute: The entire leaking pipeline system is replaced with new pipes. Older plumbing systems that have a history of leaking can benefit greatly from this fix.
- In-Place Pipe Coating: This repair uses epoxy pipe coating to plug up multiple small leaks in the plumbing system without the expense or inconvenience of uncovering the slab.
- PEX Replacement Piping: PEX stands for “cross-linked polyethylene.” A proven replacement for copper pipes, PEX piping is flexible and durable and has been successfully used for over 20 years. It won’t pit, scale, or corrode and offers excellent freeze-damage protection due to its flexibility.

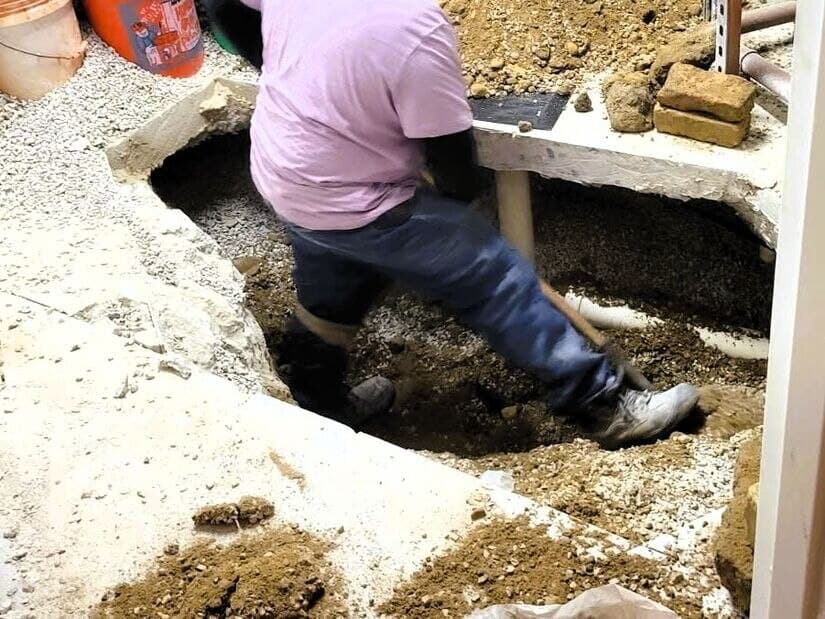
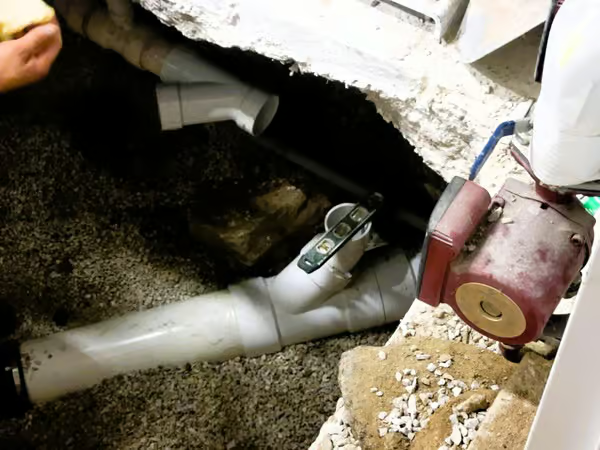
Don’t Let a Slab Leak Get the Best of You!
The bottom line here is that slab leaks are no joke. If you suspect a slab leak, the best solution is to hire a qualified professional plumber to accurately and completely diagnose the problem.
Early detection is key to preventing further damage. Remember, not all plumbers are qualified or even offer slab leak detection. Your best bet is to research the options available to you in your area and hire an expert.